Cold Gas Spray Systems
Cold Gas Spray Systems are advanced material – deposition technologies that operate based on the principle of high – velocity particle impact.
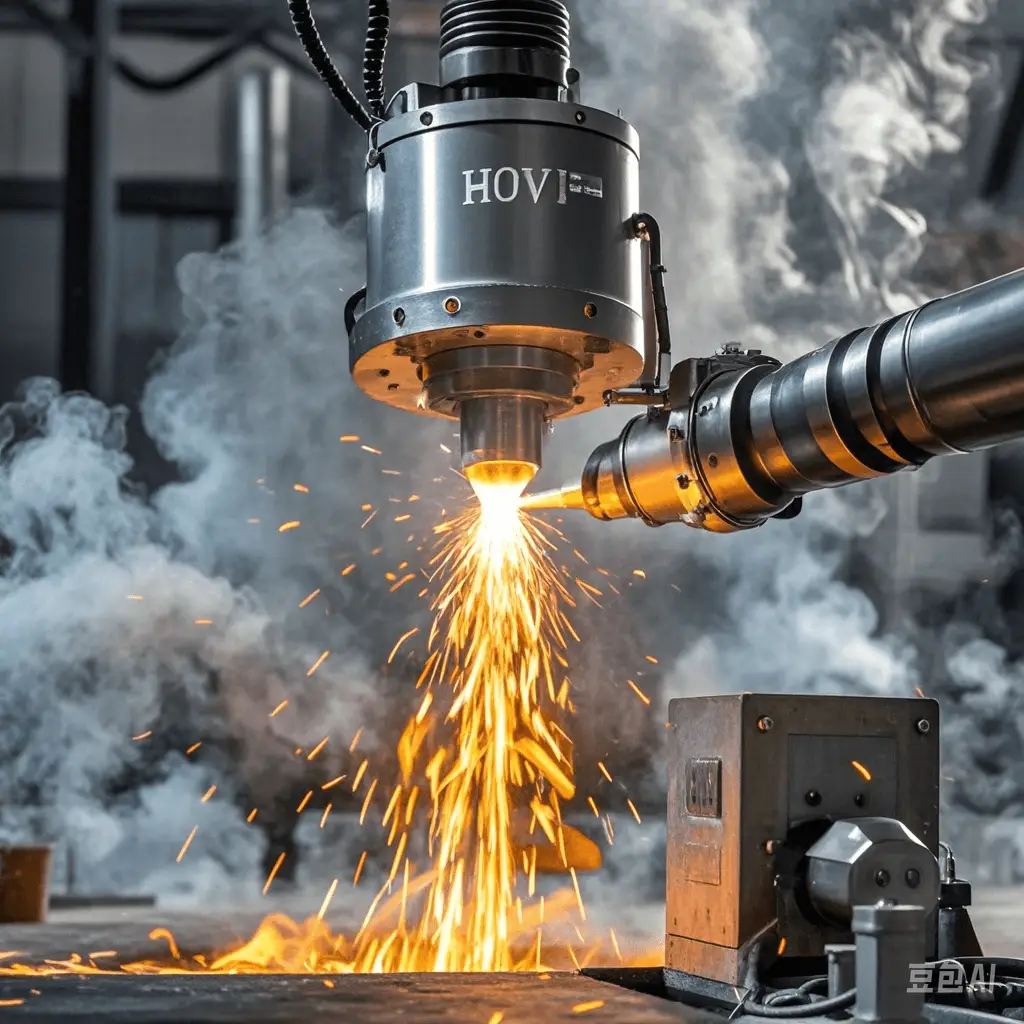
Turn-key Systems
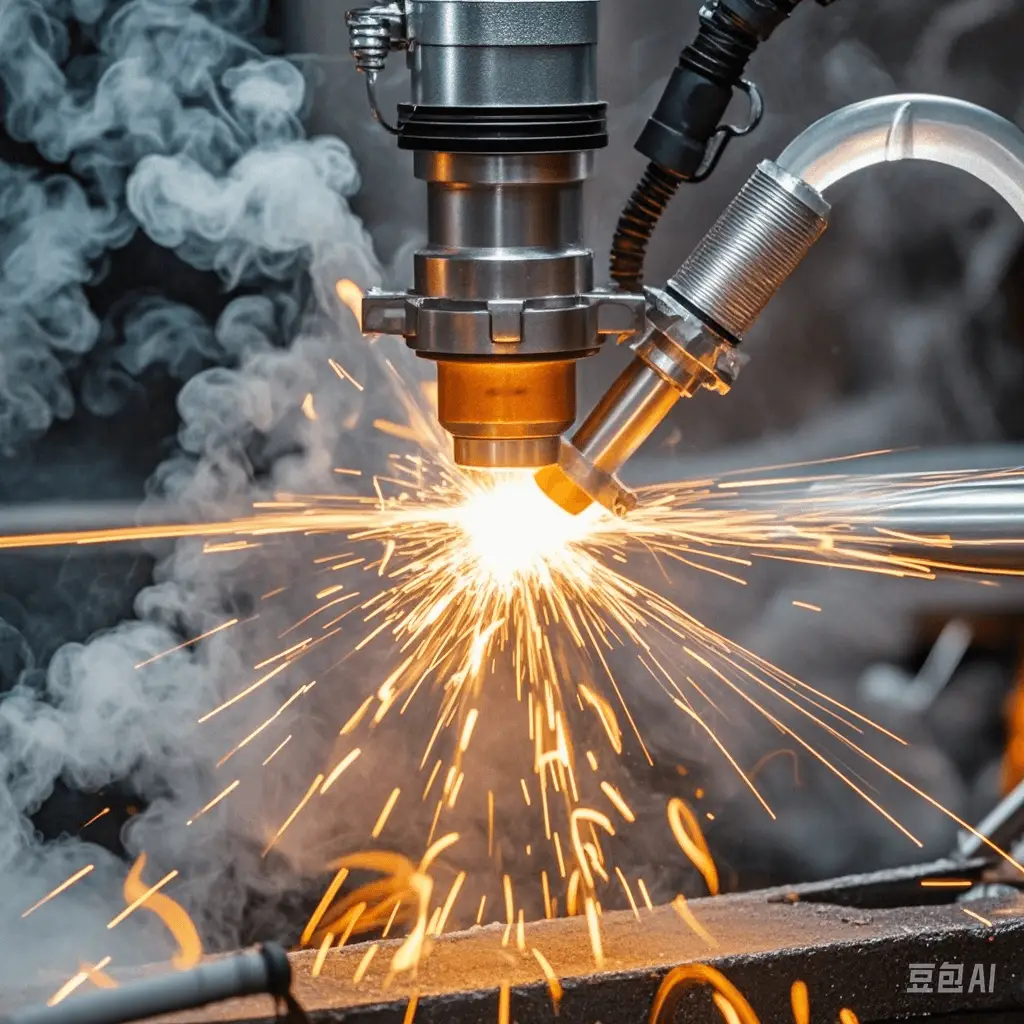
Thermal Spray Systems
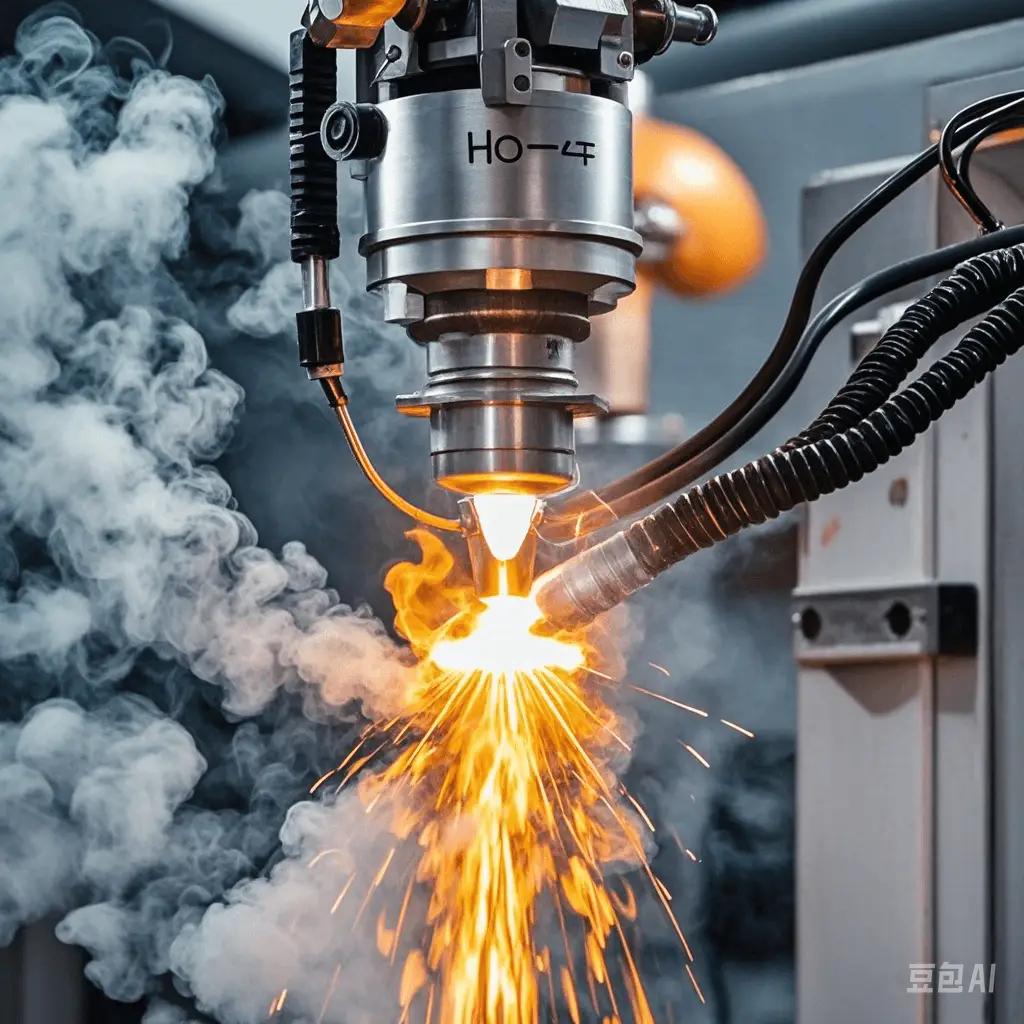
Auxiliary Equipment
1.What is the Working Principle of Cold Gas spray systems?
Acceleration of Powder Particles
In a cold gas spray system, a carrier gas (usually helium, nitrogen, or compressed air) is accelerated to high velocities, typically in the range of 300 – 1200 m/s, through a converging – diverging nozzle. Fine powder particles of the material to be deposited, such as metals (e.g., aluminum, copper, steel), ceramics, or polymers, are injected into the high – speed gas stream.
The gas – particle mixture then exits the nozzle at supersonic speeds. As the particles impact the substrate surface, they plastically deform due to the kinetic energy of impact and bond to the substrate, gradually building up a coating or a solid – state deposit. Unlike other thermal spray processes, the powder particles in cold gas spray do not reach their melting point during the deposition process. This is why it is called “cold” spray, as the coating formation occurs mainly through mechanical interlocking and metallurgical bonding at relatively low temperatures.
2.what is the System Components of cold gas spray systems?
Gas Supply and Compression Unit
This component provides the high – pressure carrier gas. For example, a helium or nitrogen gas cylinder may be used, along with a compressor to increase the gas pressure to the required levels. The gas is then filtered to remove any contaminants that could affect the quality of the deposition.
Powder Feeding System
It precisely meters and injects the powder particles into the high – speed gas stream. There are different types of powder feeders, such as gravity – based feeders and gas – entrainment feeders. Gravity – based feeders rely on the force of gravity to deliver the powder, while gas – entrainment feeders use a secondary gas flow to carry the powder into the main gas stream.
Spray Gun
The spray gun is where the powder and the high – speed gas are combined and ejected towards the substrate. It contains the nozzle, which is designed to accelerate the gas – particle mixture to supersonic speeds. The design of the nozzle is crucial, as it affects the velocity, distribution, and focusing of the particles, ultimately influencing the quality of the deposited coating.
Substrate and Manipulation Equipment
The substrate is the object on which the coating is being applied. Manipulation equipment, such as robotic arms or automated stages, is used to move the spray gun relative to the substrate. This allows for precise control of the coating thickness, coverage, and deposition pattern.
3.what is the Advantages of cold gas spray systems?
Minimal Thermal Damage
Since the powder particles do not melt during deposition, cold gas spray causes minimal thermal damage to the substrate. This makes it suitable for heat – sensitive materials, such as polymers, composites, and some high – strength alloys. For example, in the electronics industry, cold gas spray can be used to deposit metal coatings on printed circuit boards without damaging the delicate electronic components.
High – Quality Coatings
The process can produce coatings with high density, good adhesion, and excellent mechanical properties. The lack of melting reduces the formation of porosity, oxides, and other defects commonly associated with traditional thermal spray processes. As a result, cold – gas – sprayed coatings often have superior corrosion resistance, wear resistance, and fatigue properties.
Wide Range of Applicable Materials
Cold gas spray can deposit a diverse range of materials, including metals, ceramics, and polymers. This versatility makes it useful in various industries, from aerospace for repairing and coating turbine components to the automotive industry for applying wear – resistant coatings on engine parts.
4.what is the Applications of cold gas spray systems?
Aerospace Industry
Cold gas spray is used for repairing damaged components, such as turbine blades. It can deposit metal coatings to restore the dimensions and functionality of the blades without subjecting them to high temperatures that could compromise their mechanical properties. Additionally, it can be used to apply protective coatings on aircraft structures to enhance corrosion and erosion resistance.
Automotive Industry
In the automotive sector, cold gas spray can be used to coat engine components, such as cylinder liners, with wear – resistant materials like chromium – based alloys. This can improve the engine’s efficiency and lifespan by reducing friction and wear.
Electronics Industry
As mentioned earlier, it can be used to deposit conductive metal coatings on electronic components. This is useful for applications such as creating electrical connections, shielding, and improving the thermal management of electronic devices.